SILICONE VACUUM BAG
Silicone vacuum bag moulding is a hybrid process between vacuum infusion and RTM injection. It consists of placing dry reinforcements under vacuum, in a mould covered by a thick silicone vacuum bag, which will then be impregnated with the arrival of resin which is sucked up by the depression created in the mould. This technology allows the production of monolithic parts (low and high thickness), such as sandwich structures.
The advantages of the silicone vacuum bag compared with contact moulding are:
- a higher fibre rate due to the definable amount of resin used, offering a better strength-to-weight ratio.
- Parts are reproducible
- A better protection of the operators against solvent emissions such as styrene. VOC standards.
The advantages of the silicone vacuum bag compared with infusion moulding are :
- A clear reduction in consumable devices as the bag is reused to produce several parts (a few hundred).
- Greater ease of use, in particular to ensure water tightness when closing the bag.
- This technology allows the use of various matrices: unsaturated polyester, vinyl ester and epoxy.
The advantages of the silicone vacuum bag compared with RTM injection :
- Low investment
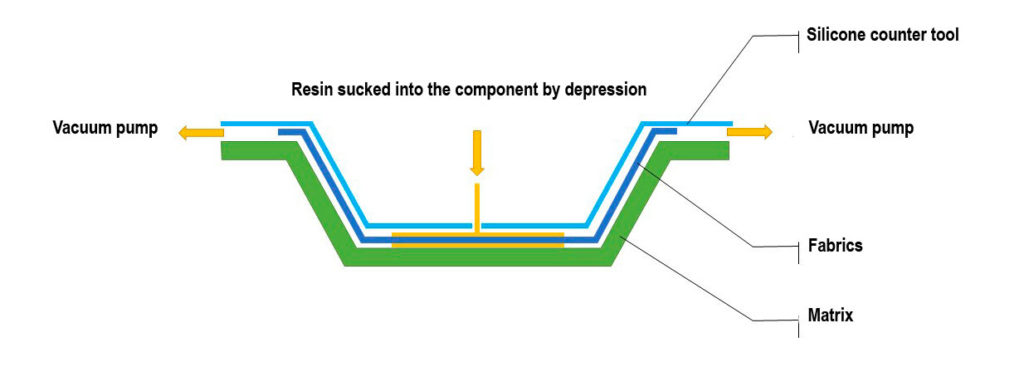
Applications
- Sports
- Campervan pavilions
- Sand yacht hulls
- Bump hoods
Avantages
- Good mechanical properties
- Numerous possibilities of shapes
- Reasonable investments
- Simple moulds
- Low VOC emissions
Disadvantages
- Only one smooth side
- Careful handling of the silicone vacuum bag
- Silicone vacuum bag life duration
- Limited part sizes